- Joined
- Apr 5, 2016
- Messages
- 130
- Likes
- 369
- Portables
- 20ish...
Hey guys what's up! Sorry this is kind of a direct copy and paste of blog post but I felt there should be a post here about this project! This is my latest completed portable Nintendo 64, with big help from @Gman and @Aurelio!
This is my 16th finished portable N64 in my almost 15 years of portable making and never would I have imagined this hobby lasting as long as it has for me, or the skillsets that followed because of it! Because this is my 5th major revision of my portable N64s, and that I'm horrible with creative names, The 5th GeN64 is were I landed.
Hope you enjoy!
Hard to believe that it’s been over 8 years since my last major design of a portable N64. I mean to put that in perspective, the portable version before that was a vacuum-formed and frankencased monstrosity that might as well have been held together with bubblegum!
But after the Cross Plane project finished up at the end of 2013, I found myself for the first time with access to new maker tools that were just starting to come within public reach. And those tools were of course, 3D printers and low volume prototype boards for custom electronics.
Although this crossed over with my CNC efforts which had begun to take hobby vacuum-forming to the next level, the ability to design from the inside out was just too enticing and thus CAD and 3D printing took over and it was only a matter of time before I circled back to the N64 with these new methods.
Fast forward now to the better end of a decade, and not only am I back with a brand new Nintendo 64 portable, but one that uses more fabrication techniques than I could have ever believed I’d have access too.
I first have to acknowledge though that this build was not a sole effort on my part, nor have most of my projects over the past decade. And in this case, I collaborated with some of the best in the business when it comes to portable making, and in fact some of those whole actually made portable making a business.

A huge heartfelt thank you is owed to Gunnar (Gman) and Aurelio of Bit Built and 4 Layer Tech for all their help with the shit I don’t understand! That of course mainly being circuit board design and firmware, to which the entire new system was based around.
TECH SPECS
While the video above does go though the system and some of its key new features, it doesn’t go too into detail with how it’s made or specifically what’s under the hood. So for those who like that kinda thing, here we go.
Enclosure – As per the standard, the base is made up of (7) 3D printed parts. A front and back face plate, a front and back face bracket, a cart cover and 2 battery covers. Also 7 bracket clamps hold the two ends together with flathead machine screws.
Buttons – The actual buttons on this one are all SLA 3D printed in clear. And though the R/L & Z buttons use the traditional soft top tack switches, the rest took advantage of having a real PCB motherboard and used the conductive rubber membranes like the pro’s use! We’ll get to that in a bit, but for the R/L & Z, I had to rethink how the best way to mount them to the case would be. Not tryin to brag, but this side-channel bracket system not only fit well with the design, but the feel and responsiveness is on par with a real controller. So simple, yet so effective!
Display – The display is the one thing that I have not changed. It uses the same 5″, 4:3 Aspect Ratio display as many others. This first set-up only uses the standard composite display, which isn’t the best but does the job.
Screen Protector – This is the first time I’ve used this technique on an N64 portable, and just like the experience I had with the Tiger Boy Advance, I found that custom artwork printed on Self-Adhesive Vinyl gave the sharpest result. This allowed for the used of a plain, non-printed, piece of CNC cut acrylic to be used as the lens itself, which simplified a lot of the cut and print process. Figuring out how to make the backlit logo shine through only when there was backlight was a bit of a challenge.
The Backlit Logo – Blocking out only certain parts of light is a challenge. My first attempt used a blank piece of CNC cut acrylic with the Nintendo logo cut out of a black self adhesive vinyl and applied to it. While this did the trick, it wasn’t as clean as I hoped and the new versions take advantage of Layered Printing, with the blackout layers built right in.
The PCBs – This of course was the big one and their design and testing took a majority of the overall time it took to get this project completed. Aside from the main motherboard, there were 3 Sub-boards specific to this design. A power/volume board at the base, an LED board for the logo back light and a backer board for the new Cart Slot FFC.
The board also was designed around (3) 4 Layer Tech boards. The “U-Amp 2”, A “PMS-Lite Rev E” and a soon-to-be released N64 controller board that uses an original N64 controller chip, but has a multiple set-up options for custom configurations as well as built in FRAM for game saves.
This particular controller config is set up for a Nintendo Joy Con control stick, with programmed dead zone and drift reduction, along with a hotkey that allows recalibration if need be.
The U-Amp is also very cool because it supports a switchable headphone jack. We all miss the headphone jack, they is no deigning! The speakers themselves are also new to me, but they are the same ones used in the original GBoy kits. Not at powerful but they work.
These three boards solder directly to the main motherboard, which makes the once tedious wiring an absolute breeze!
USB C Charging – One of the main benefits of the PMS-Lite is its ability to support USB-C charging with Power Delivery. This allows for the use of a very standard charging solution that is available almost everywhere and can really speed up the process.
New Cart Slot FFC – This is a redo of the original FFC cart slot relocation that was originally done by RDC. The problem with that version is that the trace length was really maxed on certain pins and just not a very consistent length. The video does a good job explaining what we had to do to make this work as intended!
Battery Power – The system is powered by (3) 3.7v Li/Io18650 battery cells. Originally the idea was to power it with just two, but since I’d never used them before, I had no idea how little battery life they had in comparison to the 7.4V Li/Po flat cells I used to use. I learned a few important lessons about Volts X Capacity to = Watt/hrs, so a third cell needed to be added and it was all a matter of luck that it actually fit!
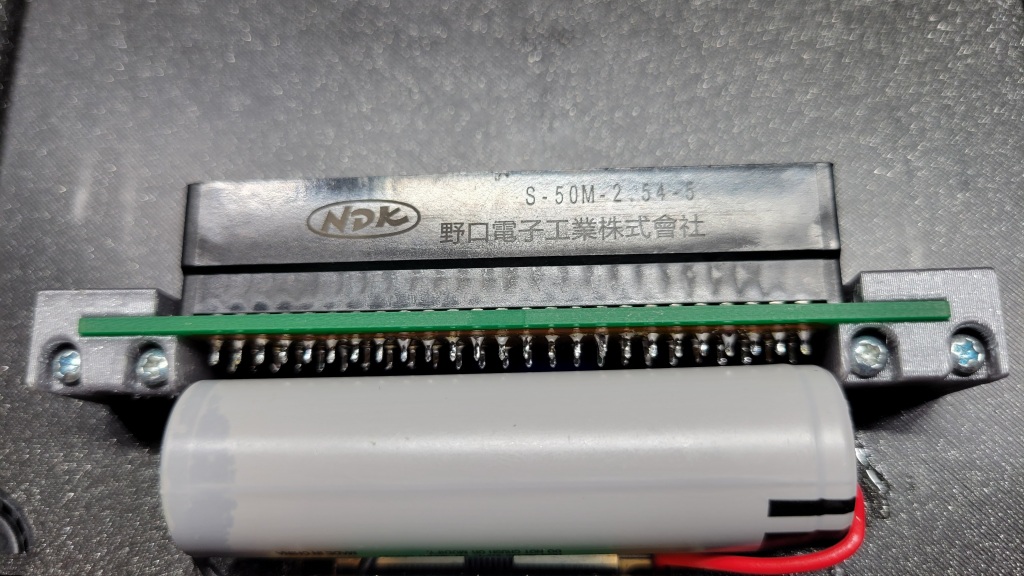
The N64 – As before, the main system is a moderately trimmed N64 main board. No crazy RCP rewiring or expansion pak relocations. Using CNC to manually trim is one of the best things ever!

I’ll more than likely be adding to this post with things I forgot or be making additional posts about this in the future, but hopefully this gives a pretty good overview of what this project took to complete! I appreciate you as always and if you have any questions or feed back, send ’em my way!
This is my 16th finished portable N64 in my almost 15 years of portable making and never would I have imagined this hobby lasting as long as it has for me, or the skillsets that followed because of it! Because this is my 5th major revision of my portable N64s, and that I'm horrible with creative names, The 5th GeN64 is were I landed.
Hope you enjoy!
Hard to believe that it’s been over 8 years since my last major design of a portable N64. I mean to put that in perspective, the portable version before that was a vacuum-formed and frankencased monstrosity that might as well have been held together with bubblegum!
But after the Cross Plane project finished up at the end of 2013, I found myself for the first time with access to new maker tools that were just starting to come within public reach. And those tools were of course, 3D printers and low volume prototype boards for custom electronics.
Although this crossed over with my CNC efforts which had begun to take hobby vacuum-forming to the next level, the ability to design from the inside out was just too enticing and thus CAD and 3D printing took over and it was only a matter of time before I circled back to the N64 with these new methods.
Fast forward now to the better end of a decade, and not only am I back with a brand new Nintendo 64 portable, but one that uses more fabrication techniques than I could have ever believed I’d have access too.
I first have to acknowledge though that this build was not a sole effort on my part, nor have most of my projects over the past decade. And in this case, I collaborated with some of the best in the business when it comes to portable making, and in fact some of those whole actually made portable making a business.

A huge heartfelt thank you is owed to Gunnar (Gman) and Aurelio of Bit Built and 4 Layer Tech for all their help with the shit I don’t understand! That of course mainly being circuit board design and firmware, to which the entire new system was based around.
TECH SPECS
While the video above does go though the system and some of its key new features, it doesn’t go too into detail with how it’s made or specifically what’s under the hood. So for those who like that kinda thing, here we go.
Enclosure – As per the standard, the base is made up of (7) 3D printed parts. A front and back face plate, a front and back face bracket, a cart cover and 2 battery covers. Also 7 bracket clamps hold the two ends together with flathead machine screws.

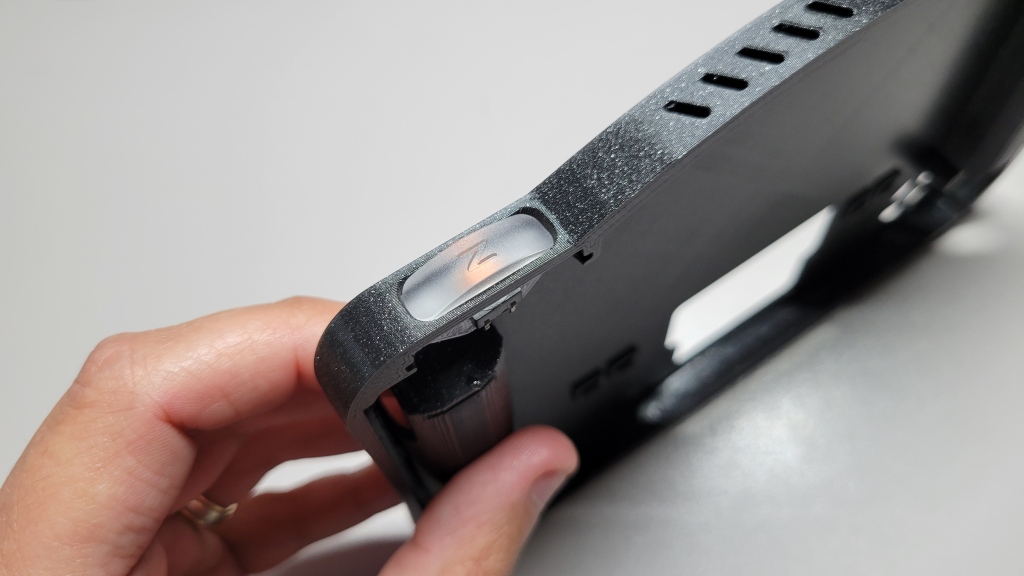





Buttons – The actual buttons on this one are all SLA 3D printed in clear. And though the R/L & Z buttons use the traditional soft top tack switches, the rest took advantage of having a real PCB motherboard and used the conductive rubber membranes like the pro’s use! We’ll get to that in a bit, but for the R/L & Z, I had to rethink how the best way to mount them to the case would be. Not tryin to brag, but this side-channel bracket system not only fit well with the design, but the feel and responsiveness is on par with a real controller. So simple, yet so effective!






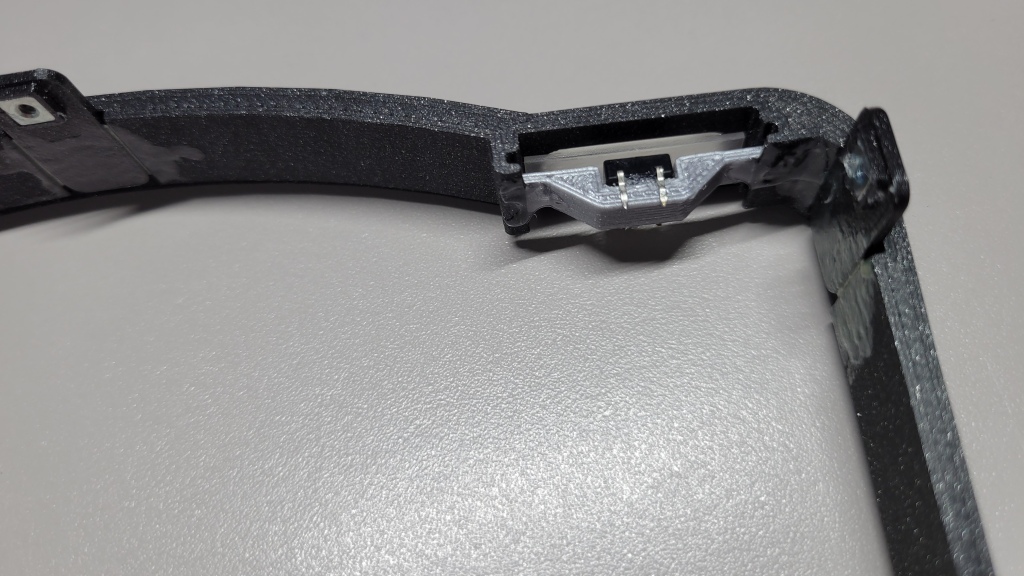
Display – The display is the one thing that I have not changed. It uses the same 5″, 4:3 Aspect Ratio display as many others. This first set-up only uses the standard composite display, which isn’t the best but does the job.
Screen Protector – This is the first time I’ve used this technique on an N64 portable, and just like the experience I had with the Tiger Boy Advance, I found that custom artwork printed on Self-Adhesive Vinyl gave the sharpest result. This allowed for the used of a plain, non-printed, piece of CNC cut acrylic to be used as the lens itself, which simplified a lot of the cut and print process. Figuring out how to make the backlit logo shine through only when there was backlight was a bit of a challenge.
The Backlit Logo – Blocking out only certain parts of light is a challenge. My first attempt used a blank piece of CNC cut acrylic with the Nintendo logo cut out of a black self adhesive vinyl and applied to it. While this did the trick, it wasn’t as clean as I hoped and the new versions take advantage of Layered Printing, with the blackout layers built right in.



The PCBs – This of course was the big one and their design and testing took a majority of the overall time it took to get this project completed. Aside from the main motherboard, there were 3 Sub-boards specific to this design. A power/volume board at the base, an LED board for the logo back light and a backer board for the new Cart Slot FFC.
The board also was designed around (3) 4 Layer Tech boards. The “U-Amp 2”, A “PMS-Lite Rev E” and a soon-to-be released N64 controller board that uses an original N64 controller chip, but has a multiple set-up options for custom configurations as well as built in FRAM for game saves.
This particular controller config is set up for a Nintendo Joy Con control stick, with programmed dead zone and drift reduction, along with a hotkey that allows recalibration if need be.
The U-Amp is also very cool because it supports a switchable headphone jack. We all miss the headphone jack, they is no deigning! The speakers themselves are also new to me, but they are the same ones used in the original GBoy kits. Not at powerful but they work.
These three boards solder directly to the main motherboard, which makes the once tedious wiring an absolute breeze!



USB C Charging – One of the main benefits of the PMS-Lite is its ability to support USB-C charging with Power Delivery. This allows for the use of a very standard charging solution that is available almost everywhere and can really speed up the process.
New Cart Slot FFC – This is a redo of the original FFC cart slot relocation that was originally done by RDC. The problem with that version is that the trace length was really maxed on certain pins and just not a very consistent length. The video does a good job explaining what we had to do to make this work as intended!
Battery Power – The system is powered by (3) 3.7v Li/Io18650 battery cells. Originally the idea was to power it with just two, but since I’d never used them before, I had no idea how little battery life they had in comparison to the 7.4V Li/Po flat cells I used to use. I learned a few important lessons about Volts X Capacity to = Watt/hrs, so a third cell needed to be added and it was all a matter of luck that it actually fit!
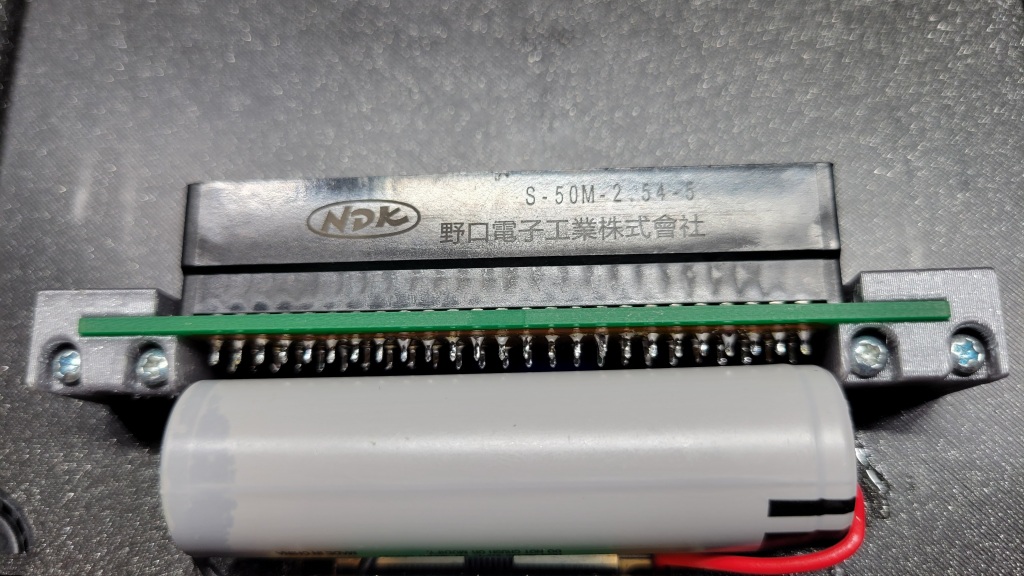
The N64 – As before, the main system is a moderately trimmed N64 main board. No crazy RCP rewiring or expansion pak relocations. Using CNC to manually trim is one of the best things ever!

I’ll more than likely be adding to this post with things I forgot or be making additional posts about this in the future, but hopefully this gives a pretty good overview of what this project took to complete! I appreciate you as always and if you have any questions or feed back, send ’em my way!